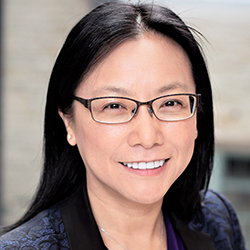
Jian Cao, NU
(Approved for Public Release)
ABSTRACT
Problem Statement: Manufacturing processes are known for their variety and complexity, particularly when integrated with new materials and new instruments. Ample historical examples point to their evolution and impacts, e.g., superplastic forming led to a tenfold increase in the formability of fine-grain metals, the combination of lithography and coating put machining and assembling onto the same platform and hence enabled the manufacture of integrated circuits, and 3D printing’s capability of generating complex freeform geometry led to tissue engineering, etc. However, the development/invention of new processes has mainly remained an ad-hoc process since no systematic ways exists to generate them.
Even with existing manufacturing processes, the practice of identifying suitable manufacturing processes for part design has largely depended on the experience of individuals and/or databases. With an aging workforce, particularly in the U.S. manufacturing sector which doubled the gap between the median age in manufacturing versus the total non-farm workforce from 2000 (1.1 years) to 2012 (2.4 years), the potential loss of manufacturing process knowledge is alarming and requires fundamental manufacturing science research to bring new insights to convert part design to feasible manufacturing processes.
Goal: This Vannevar Bush Faculty Fellowship (VBFF) proposal aims to establish a Manufacturing Process Compiler (MPC) based on fundamental physical principles of tool and material interactions, which will be able to generate new processing ideas, cover different product lengthscales from the nano- to the meter-scale, different material types ranging from metals to polymers, and production volumes from flexible customized to mass production.
Technical Approaches: As Albert Einstein said, “We cannot solve our problems with the same thinking we used when we created them,” hence five essential elements of an MPC are to be established for realizing the ambitious goal: (1) to establish a unifying process description language (PDL) expressed by tool abstractions and influence abstractions that captures the rich variety of manufacturing methods based on physical principles; (2) to develop a part attribute analyzer (PAA) that describes design in static attributes, dynamic attributes and geometric attributes which have inherent relations with processes; (3) to develop a manufacturing process synthesizer (MPS) that generates process alternatives for given part requirements expressed by a PAA based on a systematic logic representation module; (4) to establish a manufacturing process evaluator (MPE) that assesses the processes generated by an MPS using a generic simulator and multi-scale, multi-physics simulation when a new process emerges; and finally, (5) to integrate the above components into an MPC and establish an integration and demonstration testbed (IDT) that shows the feasibility of systematically synthesizing new and organizing existing manufacturing processes.
Anticipated Outcome and Impact on DoD Capabilities: This project will establish new physics based ontology for describing manufacturing processes and a manufacturing process synthesizer based on mathematical logic representation. A user-friendly integrated MPC, experimentally tested, is expected to reduce the barriers for exploring new manufacturing processes and conducting autonomous process flow optimization, and hence providing the foundation for putting highly sophisticated manufacturing knowledge from the hands of a few into the hands of many. It will help the DoD to address the technological and business challenges in point-of-need manufacturing, replace legacy parts, and build new supply chains.